
During operations, soldiers can struggle to use the tourniquets they are given on their own. The pain caused when tightening the tourniquet is sometimes so great that it is not always tightened to optimum effect. And yet without minimum pressure, a tourniquet is ineffective. The solution involves automated inflation of the tourniquet using gas.
Charlotte and Charles worked on this project every Tuesday for nearly four months. Charlotte explains:
Because of the connection that we have with the army through our IETA military status, this subject strikes a chord with us as it directly affects deployed military staff and their survival. What’s more, the subject is very experimental and this means tangible results in practice are quickly obtained. We appreciated this point. When two exciting fields like health and medicine meet that of engineering, the resulting subject is anything but disappointing!
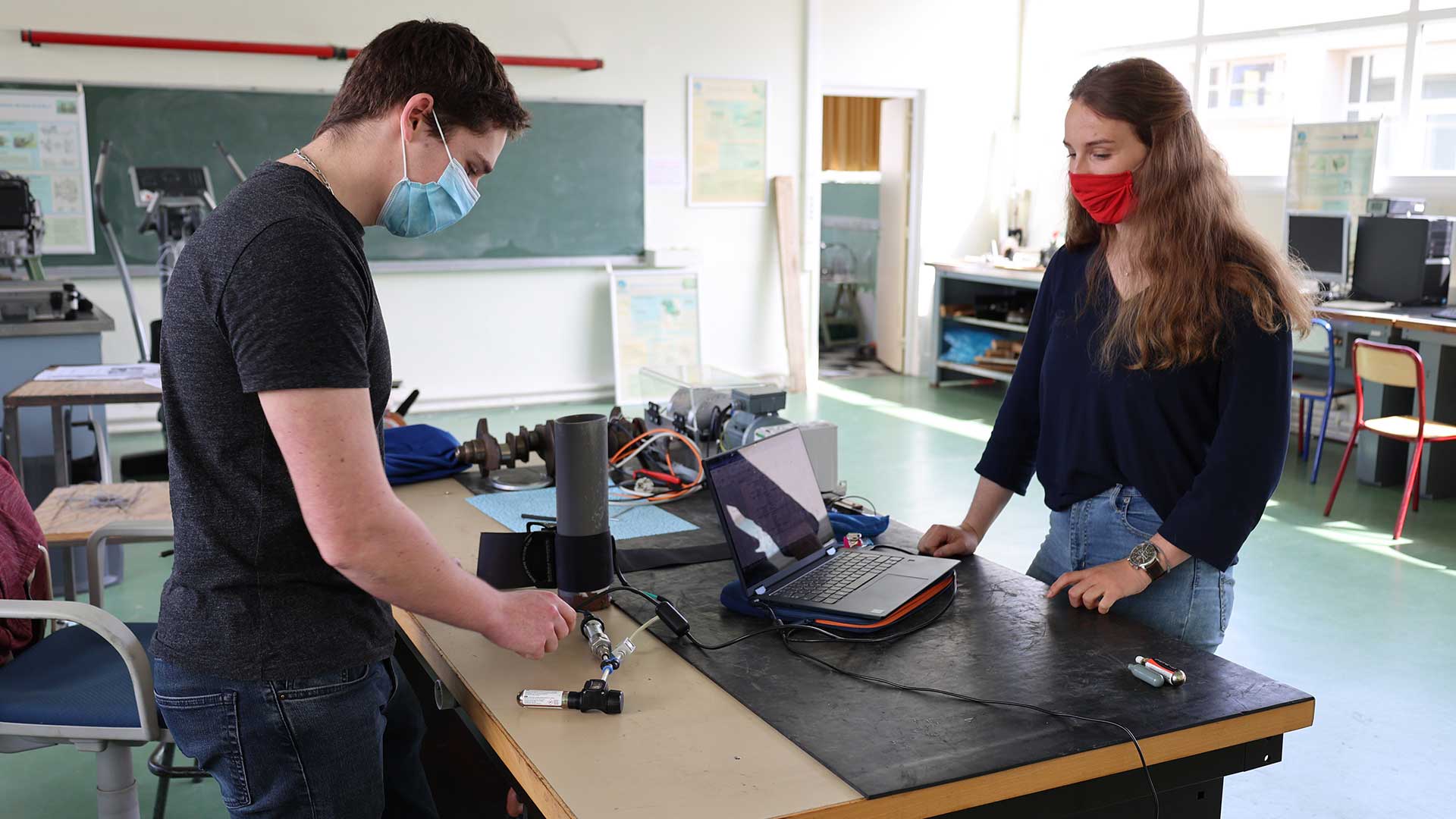
For the first stage of working out and getting to grips with the subject, the two engineering students were able to talk not only with the intern who came up with this project but also with the student who carried out studies beforehand during an internship on the subject. The team then set swiftly to work thinking about, designing and testing solutions.
A number of challenges arose:
- optimizing the weight of the device to comply with the weight restrictions laid down by the commissioning party,
- the effects of pressure loss in the tourniquet, particularly during the wounded soldier’s evacuation,
- adaptation of the device to the pressure of the gas used.
The work required a range of studies and measurements on the occlusion pressure, ideal gas models, the choice of gas, determination of the gas mass required and airtightness of the system for example.
Three prototypes designed using CATIA software were developed: one basic one, used for the first tests, a second functional one and a third one that was optimized in terms of weight with a view to being produced on an industrial scale. This one particularly includes a part for regulating flow and an anti-reverse stop system.
At the end of the project, Charles and Charlotte received the final machined parts of their second prototype and were thus able to test their device. The first tests hold out promise for a clinical trial for experimental validation of the prototype.
This is the most comprehensive project we have undertaken since beginning our engineering training. We have seen it right through from start to finish. The end result is tangible and relevant, which makes it a very rewarding experience for us," concludes Charles.